Table of Content
Fasten or “marry” each section together per manufacturer’s instructions and HUD codes. For example, if you’re moving into a park homes community, there probably isn’t a great deal to do beyond setting up your home and hooking up to the existing utilities. The community manager will probably take care of site preparation. So you’ve found a mobile home dealer you are comfortable with, bought your home on a square deal, found a site, and checked the zoning laws.

For a vertical tie-down, the anchor is installed vertically. There is a huge variety of anchors that can be installed at least five feet under the ground. If the type of soil you have is something you are unsure of, you may want to seek the help of a building inspector. The job will involve potentially dozens of people on site, all of whom will need paying.
How To Install A New Mobile Home Anchor.
They connect the home to the ground by connecting the anchor head to the beam structure of the mobile home. Tighten anchor straps tight to keep your mobile home stable and secure during high winds. Once the manufactured home is safe and secure – and deemed livable by all HUD and safety codes – the anchoring system should be set. Due to natural wear and tear, the system must be inspected for safety and surety every five to 10 years. It is important to do so to maintain the upkeep and overall protection of your manufactured home.
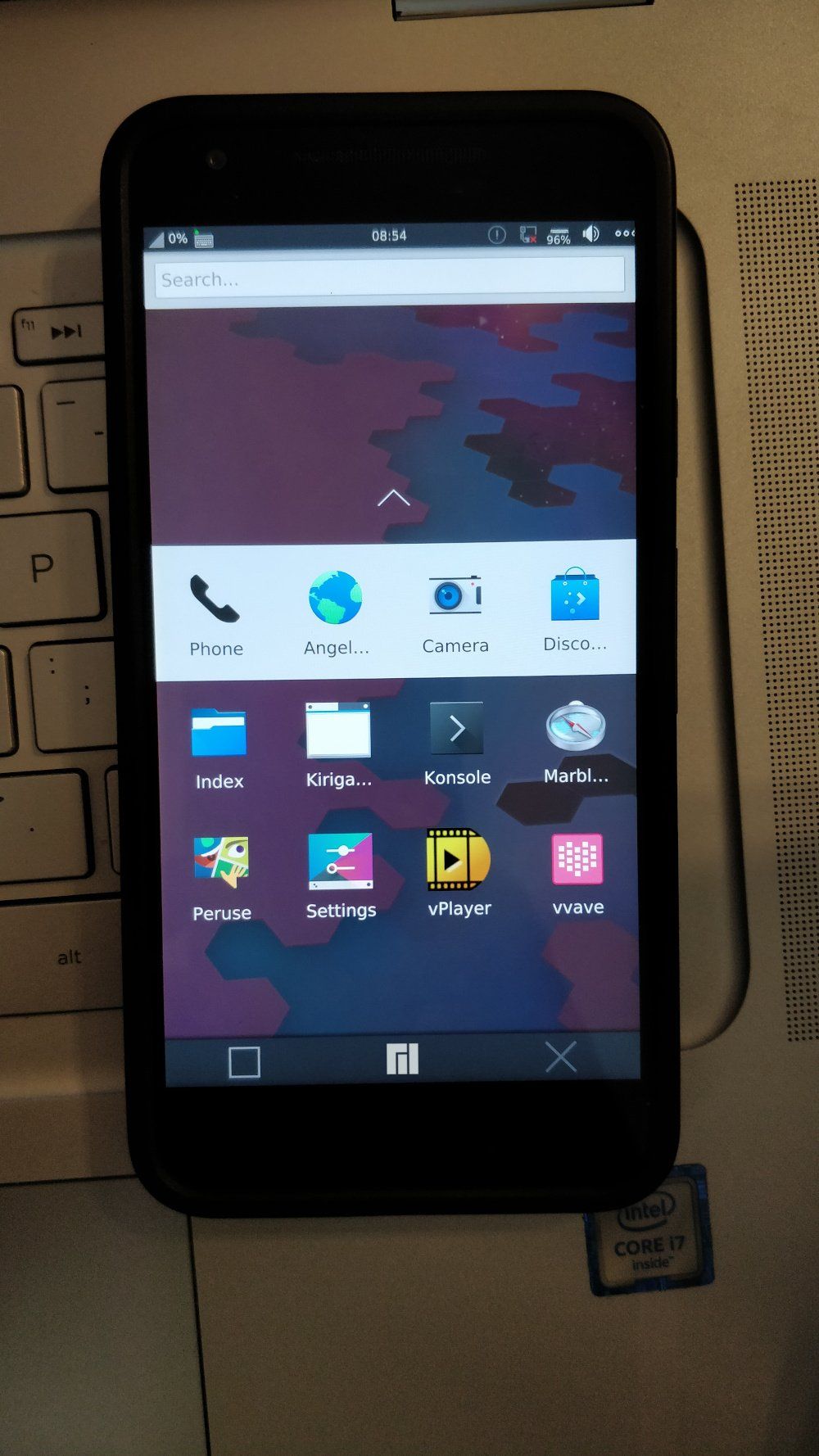
Traditional models tend to feature flat sides and ends and are built on frames. Almost all manufactured homes are elevated, situated on top of some sort of pier or foundation system, as previously mentioned. Strong, storm-force winds have the possibility of getting under the home and lifting it from the frame. In addition, the wind passing over the top of the manufactured home can create an uplift force.
How to Build a Mobile Home Support Pier – “I” Beam Foundation.
Roof racks or brackets, also known as thimbles or buffers, keep the straps locked in place from the top. Care must be taken to ensure the straps don’t block doors or windows. The type of anchor used for your home will depend on the soil condition of which the home will sit on. You’ll find anchors available for different types of soil conditions.
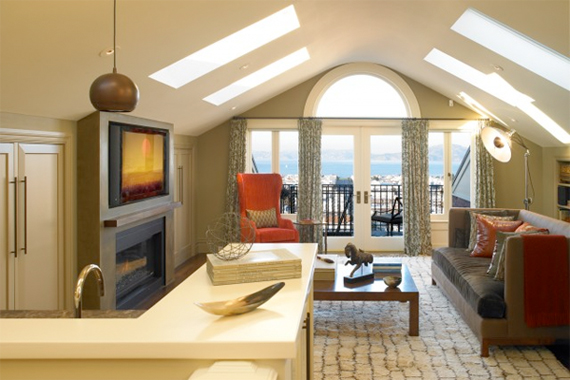
This ensures that the anchor is turned into undisturbed soil. HUD Code 3280 and 3285 require 1-1/4” X .035” or larger steel strapping conforming to ASTM D , standard specifications for strapping, flat steel and seals. Type 1, Grade 1, Finish B, with a minimum total capacity of 4,725 lbs. The straps must be provided with protections against weather deterioration and corrosion at least equivalent to that provided by a coating of zinc on steel of not less than .30 oz./ft. Slit or cut edges of coated strapping need not be zinc coated.
Tying Things Down Properly With Mobile Home Anchors
The anchor can be installed vertically if you also install a stabilization device to keep the anchor from moving sideways. A metal stabilization device can be attached to the top of the anchor and buried in the ground. Another option is to pour a concrete collar around the top of the anchor. The collar should be at least 10 inches in diameter and 18 inches deep. Whatever type of anchors you select, carefully follow the installation instructions. Auger anchors (screw-in anchors) can be installed manually by inserting a metal bar through the top of the anchor for added leverage or with a machine designed for this purpose.
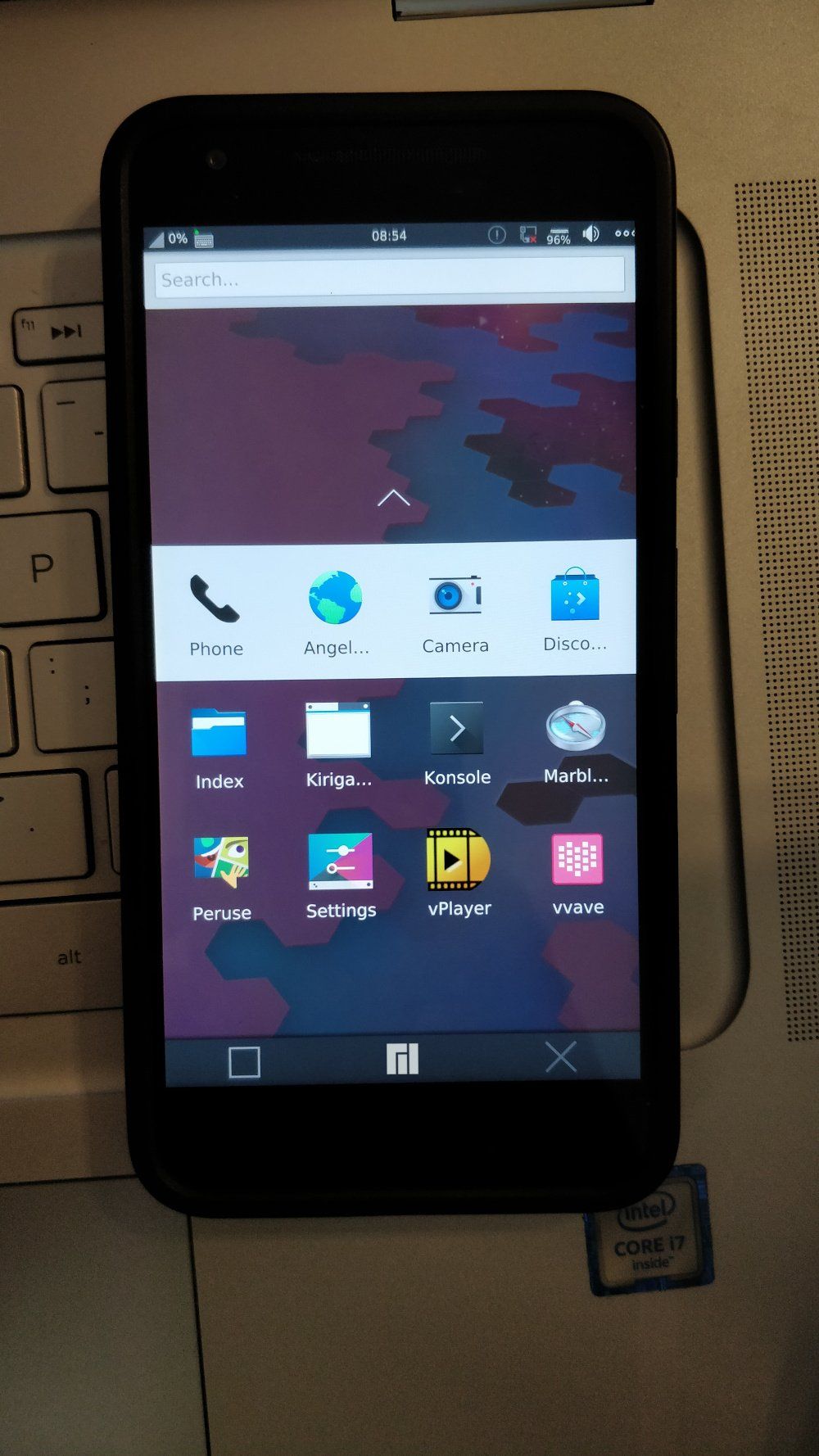
Marking and clearing the location of electric, cable, gas, water, sewer, and phone lines on the ground before installing anchors. If you have exposed over-the-top tie-downs, you must have some sort of roof protectors placed under the strap or cable at the edge of the roof. Roof protectors are also called roof brackets, buffers or thimbles. These prevent the tie-down strap or cable from damaging the roof and will prevent the edge of the roof from cutting through the tie-down.
Filling In The Anchor Hole The Right Way.
Mark the location of the anchor on the ground directly below the attachment point on the home or shed. For more information on manufactured home safety, maintenance, and general information, check out the additional resources on the Alabama Manufactured Housing Association website. Get quick tips on how to install a new awning, carport, or sunroof to your mobile home from Foremost Insurance. If your home has special site considerations, a registered professional engineer or architect can devise an alternate anchoring system. Ensure that all lines have been marked off before you begin the installation. This way, you can know where these lines are, and prevent any disaster from occurring.
One of these is setting up a way to protect the home in the event of strong winds. This can be done by tying down anchors, so the house stays secure and stable. If your jurisdiction doesn’t require inspection – and even if it does – it’s worth hiring your own home inspector. A third-party inspector goes beyond code requirements and looks at the quality of the installation work. Discovering snags and problems early means you can get them fixed before the setup crew leaves the site, and within the warranty time limits. Pricing varies from $200 to around $400 but hands down, hiring a home inspector is the best money you’ll spend for assuring the longevity and safety of your home.
Check out other posts for more safety tips and techniques. Before your home is delivered, you must make sure that the site has been prepared and is accessible. It’s a good idea to have the set-up crew visit the site before they quote for the job, so you’re both aware of any special requirements you might have to consider.
Anything more and the mobile home may not be getting the support it needs during periods of high winds or severe weather. There’s a big difference in the strength of modern mobile homes vs. older mobile homes. Working with a grounds inspector to determine the surrounding area’s soil type. The soil type will determine the type of anchor that will be used to secure the home. Manufactured homes are protected against strong winds, storms, and natural elements using anchoring and tie-down systems. Living in a manufactured home comes with many great benefits, but there are aspects to this choice that entails setting up extra safety measures.
If you will be attaching your tie-downs to a concrete foundation, make sure it is at least 4 inches thick. Installing a tie-down and anchoring system is not too complicated for most do-it-yourselfers. At the very least you should have a building inspector or a trained installer check over your finished work. It is important to note that the requirements for your local area can vary quite a bit from what is shown above.
Anchors and tie-downs that are fixed to a foundation are necessary for keeping manufactured homes in place during storms and high winds. You might have heard myths involving manufactured homes and tornadoes – some of which may have even turned you off from considering purchasing a manufactured home. But truth be told, with professional installation and proper maintenance, a manufactured home is just as dependable as any site-built home. You'll find specific installation instructions with your anchor.
You won’t be permitted to move in until the home passes inspection and the inspector issues a certificate of occupancy. This also triggers a notice to the utility company to activate power. Your set-up crew will arrange for state inspection since it is ultimately their responsibility to ensure the installation has been completed in compliance with state regulation. Steel Support Piers are designed for use as a replacement for dry stacked blocks, piers available up to a maximum of 30 inches. Steel Support Piers are designed and tested to vertical loads for a support rating of 6,000 lbs.
The number of anchors you need will vary based on your grade and other factors. Many anchors are able to accommodate both a vertical and diagonal tie down on the same anchor. Older anchors installed prior to 1997 were more than likely made of non galvanized steel which deteriorates rapidly. This is especially true in a wet area where flooding occurs and water stays under the home for any length of time. Anchors are connected to the home with galvanized steel swivel straps and a beam hook. Fully drive anchor, attach strap , and pretension strap to pull anchor rod against the stabilizer plate.
No comments:
Post a Comment